Explain the general purpose of the failure mode and effects analysis (FMEA) process.
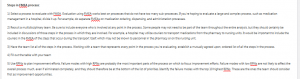
1. Describe the steps of the FMEA process as defined by IHI.
2. Complete the attached FMEA table by appropriately applying the scales of severity, occurrence, and detection to the process improvement plan proposed in part B.
Note: You are not expected to carry out the full FMEA.
Failure Modes and Effects Analysis (FMEA) is a systematic, proactive method for evaluating a process to identify where and how it might fail and to assess the relative impact of different failures, in order to identify the parts of the process that are most in need of change. FMEA includes review of the following:
· Steps in the process
· Failure modes (What could go wrong?)
· Failure causes (Why would the failure happen?)
· Failure effects (What would be the consequences of each failure?)
Teams use FMEA to evaluate processes for possible failures and to prevent them by correcting the processes proactively rather than reacting to adverse events after failures have occurred. This emphasis on prevention may reduce risk of harm to both patients and staff. FMEA is particularly useful in evaluating a new process prior to implementation and in assessing the impact of a proposed change to an existing process.
Steps in FMEA process:
1) Select a process to evaluate with FMEA. Evaluation using FMEA works best on processes that do not have too many sub-processes. If you’re hoping to evaluate a large and complex process, such as medication management in a hospital, divide it up. For example, do separate FMEAs on medication ordering, dispensing, and administration processes.
2) Recruit a multidisciplinary team. Be sure to include everyone who is involved at any point in the process. Some people may not need to be part of the team throughout the entire analysis, but they should certainly be included in discussions of those steps in the process in which they are involved. For example, a hospital may utilize couriers to transport medications from the pharmacy to nursing units. It would be important to include the couriers in the FMEA of the steps that occur during the transport itself, which may not be known to personnel in the pharmacy or on the nursing unit.
3) Have the team list all of the steps in the process. Working with a team that represents every point in the process you’re evaluating, establish a mutually agreed upon, ordered list of all the steps in the process.
4) Fill out the table with your team
5) Use RPNs to plan improvement efforts. Failure modes with high RPNs are probably the most important parts of the process on which to focus improvement efforts. Failure modes with low RPNs are not likely to affect the overall process much, even if eliminated completely, and they should therefore be at the bottom of the list of priorities. Identify the failure modes with the top 10 highest RPNs. These are the ones the team should consider first as improvement opportunities.
For the Table:
In the left-most column, input the numbered list of the steps in the process. Then, working with the members of the team who are involved in specific steps, fill out the remaining columns as follows:
o Failure Mode [What could go wrong?]: List anything that could go wrong during that step in the process.
o Failure Causes [Why would the failure happen?]: List all possible causes for each of the failure modes you’ve identified.
o Failure Effects [What would be the consequences of the failure?]: List all possible adverse consequences for each of the failure modes identified.
o Likelihood of Occurrence (1–10): On a scale of 1-10, with 10 being the most likely, what is the likelihood the failure mode will occur? o Likelihood of Detection (1-10): On a scale of 1-10, with 10 being the most likely NOT to be detected, what is the likelihood the failure will NOT be detected if it does occur?
o Severity (1-10): On a scale of 1-10, with 10 being the most likely, what is the likelihood that the failure mode, if it does occur, will cause severe harm?
o Risk Profile Number (RPN): For each failure mode, multiply together the three scores the team identified (i.e., likelihood of occurrence x likelihood of detection x severity). The lowest possible score will be 1 and the highest 1,000. To calculate the RPN for the entire process, simply add up all of the individual RPNs for each failure mode.
o Actions to Reduce Occurrence of Failure: List possible actions to improve safety systems, especially for failure modes with the highest RPNs. a) Tip: Teams can use FMEA to analyze each action under consideration. Calculate how the RPN would change if you introduced different changes to the system.
C – Describe in your own words C1 – There are 5 steps in the FMEA process according to IHI; completing the FMEA table is Step 4. A numbered list can be used. Describe in your own words.
The content to apply to the FMEA table is your Improvement Plan from B, and NOT the original Scenario errors. Your objective is to describe your plan in 4 steps in Column 1; next hypothesize a fail for each step in Column 2. You apply the scales/scoring to each fail. Then calculate the RPN for each row.
See Steps 3 & 4 of FMEA process.