Complete a four-part assessment in which you will prepare a production cost report, allocate overhead using estimated costs and cost drivers,
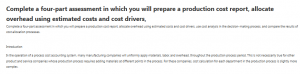
Complete a four-part assessment in which you will prepare a production cost report, allocate overhead using estimated costs and cost drivers, use cost analysis in the decision-making process, and compare the results of cost allocation processes.
Introduction
In the operation of a process cost accounting system, many manufacturing companies will uniformly apply materials, labor, and overhead, throughout the production process period. This is not necessarily true for other product and service companies whose production process requires adding materials at different points in the process. For these companies, cost calculation for each department in the production process is slightly more complex.
In some industries that use a manufacturing process operation, some units will always be lost due to shrinkage, spillage, or defects. These normal losses are expected as a necessary cost of producing high-quality products. They must be accounted for in the cost-of-production summary report. It is also possible—particularly when the process involves a liquid product— that units will be gained during production. This situation must also be accounted for and summarized in the production summary report.
Before beginning this assessment, take time to review the following topics:
Production cost report.
Activity-based costing.
Predetermined overhead allocation rates.
Quality improvement.
Allocation of service department costs.
Complete a four-part assessment in which you prepare a production cost report, allocate overhead using estimated costs and cost drivers, use cost analysis in the decision-making process, and compare the results of cost allocation processes.
Preparation
Use the Assessment 3 Template [XLSX] to complete the following four parts. Each part is a different tab in the template.
Part 1: In the template, prepare a production cost report using the FIFO method. Show all calculations and explain briefly.
Part 2: Compute overhead rate for each cost driver and production costs for each product, and compare to the consultant’s recommendations for cost drivers to explain the discrepancy between the two different approaches to product costing to management. Show all calculations.
Part 3: Compute and explain the rationale for using or not using the proposed new material based on the associated costs. Give other factors that should also be taken into consideration for this decision. Show all calculations.
Part 4: Allocate the cost to the service department using all three methods: direct, step, and reciprocal. Then comment on your findings in a paragraph. Show all calculations.
Instructions
Assessment 3 Part 1: Prepare a Production Cost Report: FIFO Method
In the template, prepare a production cost report using the FIFO method. Show all calculations and explain briefly.
Part 1 Scenario
Lamar, Inc. provides the following information for one of its department’s operations for May (no new material is added in Department T):
Lamar, Inc.: WIP Inventory: Department T
Item
Value
Beginning Inventory (16,500 units, 60% complete with respect to Department T costs)
Transferred-in Costs (from Department S)
$127,600
Department T Conversion Costs
$58,465
Current Work (38,500 units started)
Prior Department Costs
$308,000
Department T Costs
$229,955
Complete the following:
Prepare a production cost report using the FIFO method. Include an introduction.
Assessment 3 Part 2: Activity-Based Costing and Predetermined Overhead Allocation Rates
Compute overhead rate for each cost driver, production costs for each product, and compare to the consultant’s recommendations for cost drivers to explain the discrepancy between the two product costing approaches to management. Show all calculations.
Part 2 Scenario
Bath Fixtures Supply, Inc. (BFSI), manufactures three types of fixtures: industrial, standard, and brass. It applies all indirect costs according to a predetermined rate based on direct labor-hours. A consultant recently suggested that the company switch to an activity-based costing system and prepared the following cost estimates for year two for the recommended cost drivers.
BFSI: Costing System
Activity
Recommended Cost Driver
Estimated Cost
Estimated Cost Driver Activity
Order Processing
Number of orders
$59,400
200 orders
Production Setup
Number of production runs
$237,600
100 runs
Materials Handling
Pounds of materials used
$396,000
132,000 pounds
Machine Depreciation and Maintenance
Machine-hours
$316,800
13,200 hours
Quality Control
Number of inspections
$79,200
45 inspections
Packing
Number of units
$158,400
480,000 units
Total Estimated Cost
$1,247,400
In addition, management estimated 7,500 direct labor-hours for year two.
Assume that the following cost driver volumes occurred in January, year two:
BFSI: Cost Driver Volumes
Industrial
Standard
Brass
Number of Units Produced
66,000
26,400
9,900
Direct Materials Costs
$42,900
$26,400
$16,500
Direct Labor-Hours
450
450
600
Number of Orders
12
9
6
Number of Production Runs
3
3
6
Pounds of Material
16,500
6,600
3,300
Machine-Hours
638
140
80
Number of Inspections
3
3
3
Units Shipped
66,000
26,400
9,900
Actual labor costs were $15 per hour.